PROTECT EVERY BODY PART, PROTECT YOUR BOTTOM LINE.
What makes your operation run the most efficient and be the most productive? To be clear, it is not machines or other tools. It is your people. And just like your equipment, your people need to be protected at all times. As a facilities manager, it’s important to keep in mind that when you protect your employees, you also protect your bottom line. To ensure that your employees, or others visiting your facility, are protected from hazards, it’s very important to address your commitment to the Hierarchy of Controls. This tiered set of safety procedures offers facility managers a checklist of sorts that outlines the steps and efforts you can take to create the safest environment possible for employees.
WHAT EFFORTS CAN YOU MAKE TO MAKE THE SAFEST ENVIRONMENT POSSIBLE?
Starting with elimination, consider what physical objects have a potential for creating injury and remove them from the area. Then, think about what can be substituted in its place. You should also think about relocating people from the hazard and reorient where your teams operate. In doing so, you may find that they work more efficiently. Another option is to control how people work. If there is a better and safer way for them to do their jobs, teach it to them. Personal protective equipment is something many industrial workers wear out of an abundance of safety, but actually, PPE should be your last resort. Unfortunately, many facility directors choose to distribute PPE to protect their employees from danger instead of addressing issues before it’s needed. So before reading on, take a moment to think about whether your teams have executed due diligence in the area of these controls and decide if there are ways to improve safety as well as performance. When you find ways to be more intentional around the workplace, you’re able to keep people engaged in their work, boost morale, and elevate productivity and safety.
When it comes to PPE, or personal protective equipment, you can help improve operational efficiency by reducing the risk of injury and illness among workers – the benefits of which are immeasurable. From fewer lost workdays to better use of raw materials to reduced medical expenses and less need for workers' compensation, every bit helps. When you provide workers with the appropriate protective equipment, you give them confidence that translates into higher performance and a happier workforce.
When we consider the standard for PPE, it is helpful to examine what OSHA says about the use of it. Found in 29 CFR 1910.132, OSHA explains: “Protective equipment, including personal protective equipment for eyes, face, head, and extremities, protective clothing, respiratory devices, and protective shields and barriers, shall be provided, used, and maintained in a sanitary and reliable condition wherever it is necessary by reason of hazards of processes or environment, chemical hazards, radiological hazards, or mechanical irritants encountered in a manner capable of causing injury or impairment in the function of any part of the body through absorption, inhalation or physical contact.”
Choosing the PPE that works for your employees.
As the responsibility to reduce the potential risk of injuries and illnesses in the workspace falls to you, we’ve created this guide to give you a good idea of how to approach PPE should you need it.
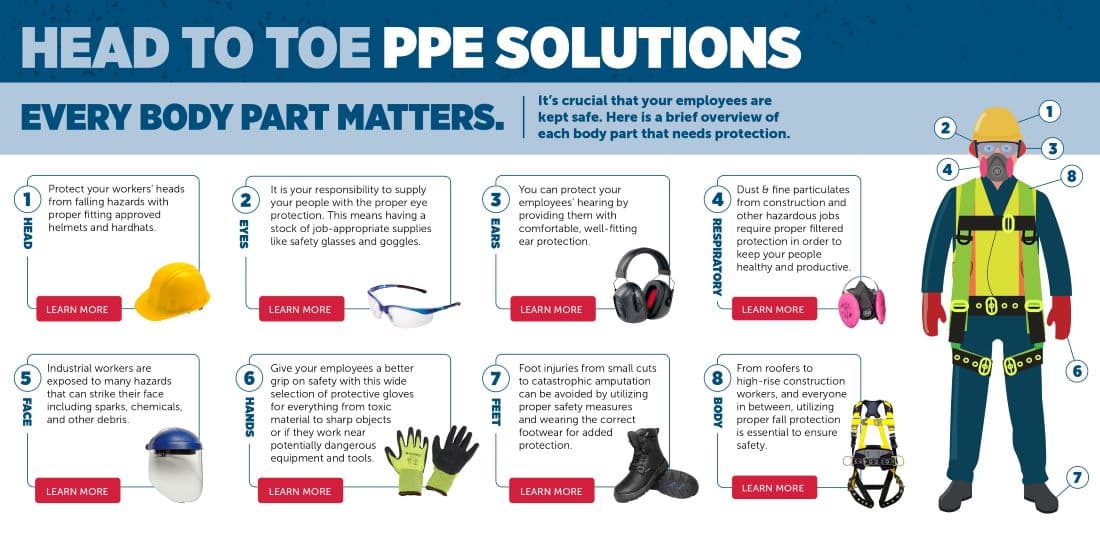
As a quick reminder, PPE is to be used in conjunction with proper training and proper fit and function of the PPE. We have found that one of the best ways to know which PPE works best is to ask those who use it. Getting your employees’ input on PPE can go a long way to making them feel included and valued regarding their personal safety on the job. Therefore, in order to have an effective PPE program, you need to garner most of your important information about safety from real-world employee experience. It’s a good practice to have employees try on various types of equipment to give you real-time feedback about comfort, durability, wear and tear and protection.
EVERY BODY PART MATTERS
Cited as the top danger in industrial settings by OSHA for the past three years, the need for protection against falls cannot be overstated. Fall protection is so important that there is a National Safety Stand-Down each year to bring focus and awareness to the issue. In 2021 slips, trips, and falls accounted for 850 deaths across all occupations. Look around your facility for potential hazards and remember the use of fall protection is required when working above 4 feet in General Industry and 6 feet in Construction. Keeping the ABCs of Fall Protection in mind is a good start. You need an Anchorage Point (Example is a Beam Clamp), Bodywear (Harness), and Connector (Self Retracting Life Line SRL), along with the proper headgear and pads.
When considering employees falling, it makes sense to consider what can fall on them or come in contact with them, from dropped objects to low pipes or racking to moving machinery,forklifts, and tools. These all can cause serious injury or death. In many cases the use of bump caps (a small and less protective piece of head protection) and hard hats can protect your workers.
In addition to things falling in the air is what’s floating in it. On the job, there are so many unhealthy elements we breathe. That is where respiratory protection comes in. Respiratory protection has also been in the OSHA Top 10 cited standards for the last five years. Protect your employees from dust and dirt, chemical vapors, welding fumes, and even biological hazards with the proper masks. But as always, first check to see if there’s something you can do to eliminate or at least reduce the exposure to anything hazardous.
Along with the lungs, the face and eyes are just as susceptible to particles in the air – and the damage from these things can be permanent. Face shields, welding helmets, googles, and safety eyewear will protect the employee from dust and chemical splash, weld splatter, flying objects, heat/cold and even radiation in the form of ultraviolet light from the sun and from welding.
Industrial settings are very loud places and noise is a very serious occupational hazard. Often, the effects of noise are not realized until decades later, and it is too late to protect the employee. Even if the noise level is under the OSHA Hearing Conservation requirement of 85 dB, damage is still occurring. A good set of ear plugs or ear muffs can do wonders to protect your workers.
When we think of protecting people we often default to the extremities, but it’s just as important to guard the body and legs as well. In many cases, the same risks and hazards mentioned above can impact one’s body. Flame retardant shirts and pants protect against electrical burns. Aluminized jackets and hoods reflect heat. Dust and chemical splash suits give immediate protection from accidental spills or during emergency clean-up. High-visibility vests and suits bring attention to the employee and signal to vehicle operators to slow down and to give them space.
Hands are always in the proverbial line of fire when it comes to injuries on the jobsite. Workers handle everything from toxic material to sharp objects and place their hands near potentially dangerous equipment and tools. You can give them a better grip on safety with this wide selection of protective gloves to guard against anything from a simple cut to muscle strains, chemical burns, and broken bones. There is a wide range of glove types for both men and women that offer varying levels of protection to match the job… well, at hand.
A recently published article can give you deeper insight into the difference you can make when it comes to hand protection for your employees - read it here.
Last but certainly not least, keeping employees’ toes and feet safe is critical. Today’s work shoes go well beyond merely offering steel toed protection. They are now designed with steel or an alternative shank that protects the rest of the foot from puncture. Many are made with anti-slip soles to mitigate falls, and some have a non-conductive sole for protection against electrical grounding. Still others offer a full rubber boot to protect from water or chemicals.
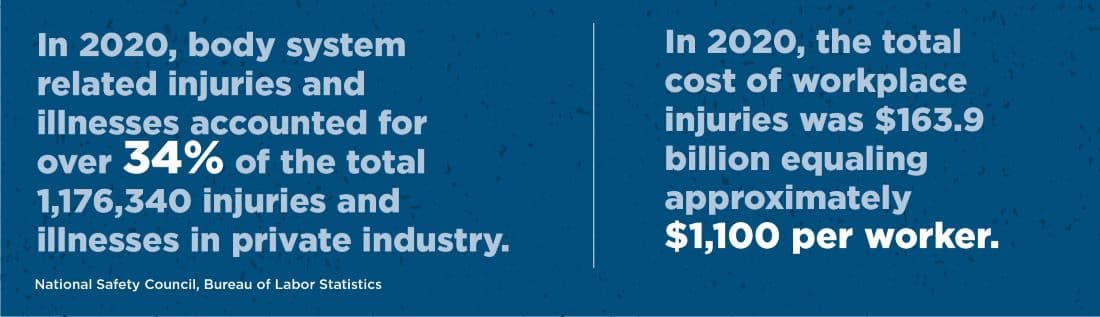
EQUIPMENT IS ONLY THE BEGINNING.
Protecting your employees properly is part of an effort to create a real culture of safety. There should never be a time when protection isn’t at the forefront of everything you do. Look for every opportunity to review proper machine operation and reinforce precaution measures everywhere in your facility as well. By properly outfitting employees and verifying they are wearing their PPE correctly, you make your operation more attractive to new candidates when they learn that you maintain a workplace that is supportive and protective.
Of course, no job site can be made perfectly safe. However, combining proper safety equipment with a genuine, operation-wide commitment to safety can reduce the risk of injury and help mitigate liability. It also goes a long way toward seeing everyone embracing accountability and taking responsibility for the well-being of themselves and each other.
Learn more about how we can help you elevate safety throughout your organization by connecting with one of our Global Industrial sales representatives at 1.888.645.0878 or contacting us here.
The information contained in this article is for informational, educational, and promotional purposes only and is based on information available as of the initial date of publication. It is the reader’s responsibility to ensure compliance with all applicable laws, rules, codes and regulations. If there is any question or doubt in regard to any element contained in this article, please consult a licensed professional. Under no circumstances will Global Industrial® be liable for any loss or damage caused by your reliance on this article.